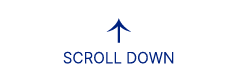
기업부설연구소
성일에스아이엠은 임직원 모두가 함께 성의(sincerity), 신의(faith), 창의(creativity)의
핵심이념을 품고 글로벌 선도기업을 만들기 위해 최선의 노력을 다하고 있습니다.
(주)성일에스아이엠 기술연구소 전용 연구시설 공장 보유
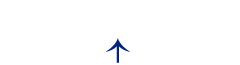
-
벤딩표준화
국내에서 최초로 유도가열벤딩기를 개발한 기술을 지속적으로 발전시키고 벤드에 적용하여 품질을 더욱 향상시키고 있습니다. 새로운 재질이나 규격을 벤딩할 경우에도 축적된 기술력을 바탕으로 공정 인자를 선정하고 연구하여 최적의 품질을 실현합니다.
벤드를 제작하는데 그치지 않고 숙련된 연구 인력으로 구성된 기술팀은 선정된 제품에 대해 세계최고 수준의 계측, 실험 시스템을 통해 고도의 분석과 시험을 거쳐 고객이 신뢰할 수 있는 정량적 계측 자료를 제공하고 있으며 이를 바탕으로 진보된 공정인자를 선정하고 연구하여 최적의 품질을 실현합니다. 또한 관련 연구기관과의 지속적인 공동연구를 통해 세계적인 표준을 수립하고 있습니다. -
ASME 코드개정
(American Society of Machnical Engineers)
성일에스아이엠은 안전성관련 배관에 장애가 되었던 국제 기술표준 ASME 개정으로 적용을 위한 기술적 배경을 확보하였습니다.
(ASME에 따른 원자력(Sec.III)과 화력 BOP 배관(B31.1)의 소반경 벤드 적용) 기존: 최소반경 3DR 이상 권유벤딩전 두께 증육 30% 이상 권유 변경: 최소반경 1.5DR 이상, 벤딩전 두께 증육 14% 권유 벤딩전 두께는 제작사의 기술정도에 따라 두께 증육을 하나,
성일에스아이엠의 기술은 1.5DR의 경우 압축벤딩을 적용하여 두께감소율을 9% 이하로 제작이 가능하며, 원자재비 구매 비용을 절감할 수 있습니다. 관련 코드의 개정에 따라 안정성 관련 소반경벤드에도 활발한 적용이 예상됩니다. -
정압기 개발
(국산화)
한국가스공사의 전국 가스배관망의 곡관부분에 대하여
고주파밴딩의 신기술과 PE코팅을 적용하여 수십년간 납품하여 품질의 건전성이 유지되도록 일조하였으며,
최근에는 한국가스공사의 권유로 전량 수입에 의존하던 정압설비의 수입대체를 위해 연구개발을 진행함.정압기 국산화 개발 핵심원천기술 확보로 정압설비 및 관련부품 수입대체로 외화절감 및 국내 공급업체 상생협력이 가능하며, 국산 고품질의 정압설비 수출 교두보를 마련함. 개발 및 시험 운전을 완료했으며 내구성 향상, 조립시간 단축, 소음감소 등 성능향상을 위한 추가개발 진행 후 상용화 하여
세계시장 진출 준비중임.[정압설비]
[정압설비 구조]
-
로봇용접
(SIMART)
공정혁신을 위한 계획생산 및 스마트팩토리 시스템을 도입하여 배관 업계 스마트 제조의 새로운 모델을 개발하고 새로운 길을 제시하고 있습니다.
스마트공장 및 자동화 시스템을 구축하여 Size, Thickness, Materials 등 다양한 규격으로 인해 도입 및 적용이 쉽지 않은 배관 제작 분야에 로봇용접과 계획생산을 도입하였습니다. 이를 통해 작업 인력 감소에 대처하고 자동화를 통한 원가절감으로 글로벌 선도업체로 전제적 진입하고 있습니다.■ 생산성 향상으로 인한 원가경쟁력 향상
■ 생산 통제, 근로환경 변화 대응, 불확실성 해소
■ 품질 신뢰도 향상, 추적성 강화